Мы пока не открылись,
скоро состоится открытие. Первым клиентам скидки!
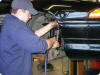
carsrepair@yandex.ru
|
|
Переборка двигателя во фрязино
Двигатели попадают в ремонт больше по причине увеличенного
расхода масла, чем от неудовлетворительных тяговых характеристик.
Износ колец внешне проявляется как повышенный зазор в их
замках, изначально составляющий в среднем 0,2–0,45 мм, к капитальному ремонту достигающий величины 3–3,5 мм и более.
«Потери» металла по радиальной толщине наблюдаются больше у
замка и противоположной его части, что связано с неравномерным давлением
поверхности колец на стенки цилиндров.
По высоте кольца изнашиваются столь незначительно, что не
было еще случаев их замены по этому поводу. Повышенный износ колец вызывает
некачественное или не вовремя меняемое моторное масло, а также неисправность
инфраструктуры очистки поступающего в цилиндры воздуха. Первая причина, кроме всех
прочих неприятностей, вызывает залегание (закоксовывание) колец в канавках
поршня — трудно устраняемый дефект без разборки ЦПГ. Ресурс поршневых колей
отечественных двигателей, исходя из многих факторов на него влияющих, находится
в широких пределах и составляет в среднем 80–150 тыс. км. 2. Поршни. Ресурс
отечественных поршней несколько превышает ресурс колец и составляет около 200–250
тыс. км. Износ поршня проверяется в основном в трех его местах:
1.Отверстие под поршневой палец. В процессе эксплуатайии
предельный зазор в сопряжении палец-поршень (в среднем около 0,05 мм) при изначально правильной сборке практически не достигается.
2. Проточки под поршневые кольца. Износ в основном
затрагивает проточку под верхнее компрессионное кольцо, так как основную
нагрузку принимает именно эта «парочка». Также как в случае с отверстием под
палец, износ определяется по зазору, который достигает предельно допустимой
величины (в большинстве случаев 0,15 мм) при пробеге в среднем 220–250 тыс. км.
3. Юбка поршня. Износ проверяется в сопряжении юбка поршня —
цилиндр. В нашем случае предельно допустимый зазор в 0,15 мм достигается при пробеге в среднем 200–220 тыс. км (дизельные двигатели требуют расточки блока
уже при зазоре более 0,1 мм).
3. Шатуны. Так как «жигулевские» шатуны в верхней части не
имеют подшипника (палец запрессовывается на «горячую»), изнашиваться
практически нечему, поэтому их ресурса обычно хватает на все время эксплуатации
двигателя. Шатуны, в верхней головке которых имеется втулка, ремонтируются ее
заменой. Новую втулку запрессовывают и разворачивают разверткой в специальном
приспособлении для получения приемлемой перпендикулярности оси поршневого
пальца к плоскости движения шатуна. Втулка служит довольно долго и, как
правило, меняется не в связи со своим износом, а по причине замены поршневого
пальца во время капитального ремонта двигателя.
4. Блок цилиндров. Изнашивается в основном в районе верхней
части цилиндров. Величина износа определяется по размеру эллипса в районе ВМТ
верхнего поршневого кольца (эллипсность должна быть не более 0,14 мм для диаметра поршней 76–79 мм) и зазору между юбкой поршня и цилиндром. ВАЗовские цилиндры
блока имеют два ремонтных величины (увеличение на 0,4 мм и 0,8 мм), а также возможность для запрессовки специальных ремонтных вставок (гильз либо
пластин) с последующей их расточкой до номинального величины. Ресурс поверхности
цилиндров в первую очередь определяется возможностью работы в нем поршневых
колец и составляет нередко 200–230 тыс. км при их замене после пробега 90 -120
тыс. км.
5. Коленчатый вал. Предельный износ коленчатого вала
наблюдается, прежде всего, в районе шатунных шеек как
наиболее нагруженных возвратно поступательными движениями
механизмов ЦПГ.
В результате длительной работы сечение шеек коленчатого вала
представляет собой эллипс, допустимая величина того составляет в среднем 0,03 мм. Шейки — как шатунные, так и коренные — перешлифовываются на ремонтные размеры (уменьшение от
номинального величины на 0,25; 0,5; 0,75 и 1,0 мм). Средний ресурс вала до ремонтного шлифования составляет 220–250 тыс. км.
рекомендуется учитывать, что после шлифования шеек их ресурс
несколько снижается (относительно шеек номинального величины). При шлифовке на
последний ремонтный размер (1,0 мм) вал «ходит» в среднем около 100 тыс. км.
Связано это с глубиной термообработки рабочей поверхности шеек (токами высокой
частоты). Слой «твердого» металла даже теоретически не превышает 2–3 мм, на
практике же он может быть значительно меньшим. К тому же существует вероятность
неравномерности слоя по его твердости.
Имеется возможность восстановить полностью изношенные шейки
методом наплавки с последующей шлифовкой под номинальный размер, но к таким
валам нужно относиться с осторожностью, так как нанесение металла на чугунную
поверхность шеек — весьма сложная операция, доступная только в
специализированных организациях. Реанимированные таким образом несколько валов,
встретившиеся нам в процессе работы, имели сетку микротрещин на поверхности
поработавших шеек. Один из дефектов коленчатого вала после кустарного
восстановления проявлялся только на полностью прогретом двигателе, при этом
стартер не мог проворачивать вал до его остывания. Причиной этого, как показал
анализ, являлся временный изгиб вала по его оси вращения от температуры
прогревшегося двигателя, так что наплавкой по возможности увлекаться не стоит.
Коленчатый вал также подвержен износу от контакта с упорными
полукольцами, ограничивающими его осевое перемещение. Повышенный зазор в этом
сопряжении (более 0,35 мм) обычно легко устраняется ремонтными полукольцами,
которые, как правило, важны только после
пробега в 200–250 тыс. км (при меньшем пробеге достаточно
поменять их на новые номинального величины).
6. Вкладыши коленчатого вала. Ресурс вкладышей, несмотря на
гораздо меньшую твердость их рабочей поверхности, превышает ресурс шеек
коленчатого вала. На практике вкладыши меняют по состоянию зазора в сопряжении
шейка — вкладыш, предварительно замерив размеры деталей (максимально допустимый
зазор для коренных подшипников составляет 0,15 мм, а для шатунных 0,1 мм), но есть смысл производить их замену при каждом капитальном ремонте
ЦПГ. Дело в том, что мягкий рабочий слой вкладышей имеет тенденцию накапливать
в себе твердые частицы продуктов износа механизмов двигателя, занесенных в
зазор посредством загрязненного масла, которые, несколько выступая над
поверхностью антифрикционного слоя подшипника (как некое подобие резцов),
нещадно «полосят» поверхность шеек.
7. Маховик двигателя. Первоначально износ появляется на его
зубчатом венце, ресурс того обычно заканчивается к пробегу 200–220 тыс. км.
Венец — деталь съемная, поэтому на ресурс самого маховика она влияния не
оказывает. Износ контактной поверхности с диском сцепления также вполне
устраним проточкой на токарном станке. Исходя из практики, маховик обычно
служит не менее, чем сам двигатель.
8. Распределительный вал. Прежде всего подвержены износу кулачки,
затем шейки и в последнюю очередь корпус подшипников, в котором он вращается.
Средний «пробег» распределительного вала находится в пределах 80–90 тыс. км.
Исходя из этого ресурса, можно определиться с ресурсами рычагов привода
клапанов и корпуса вала, потому как эти детали подлежат замене только в
комплекте. Корпус подшипников, несмотря на его значительный ресурс, меняется по
той причине, что подобрать подходящий по величиным распределительный вал — очень
непростая задача.
9. Привод распределительного вала. Детали привода: цепь и ее
звездочки — в среднем служат 80–120 тыс. км и меняются в комплекте, как
правило, по причине износа цепи. Замена башмака натяжителя и успокоителя цепи
осуществляется попутно с заменой колец, не учитывая его
остаточный ресурс.
Если привод вала осуществляется зубчатым ремнем, его меняют
по рекомендации завода-изготовителя профилактически, совместно с натяжным
роликом (в среднем, после пробега в 60 тыс. км). Если приводные шестерни ремня
ГРМ несколько изношены, сроки его замены необходимо соответственно сократить,
так как на некоторых двигателях при его обрыве клапаны и поршни обязательно
встретятся.
10. Головка блока цилиндров. Ресурс головки, если ее не
перегревать, равен ресурсу блока двигателя, так как направляющие втулки стержней
клапанов и их седла — детали заменяемые, а остальное износу практически не
подвержено. Ресурс направляющих втулок близок к ресурсу стержней клапанов и
составляет в среднем 220–250 тыс. км. Герметичность сопряжения поясок тарелки
клапана — седло клапана на практике сохраняется до пробега 130–150 тыс. км, по
этой причине при замене комплекта поршневых колец имеет смысл попутно
произвести профилактическую операцию по притирке данных сопряжений.
Ресурса седел клапанов, как правило, хватает на весь срок
эксплуатации двигателя, если после каждой замены втулок и клапанов подправлять
контактную поверхность специальными шарошками, а не притирать новое сопряжение
с помощью абразивной пасты, что многие ошибочно делают (это вызывает напрасную
потерю значительной части металла как седел, так и клапанов).
Пружины клапанов столь долговечны, что их замены на всем
протяжении эксплуатации двигателя — большая редкость в практике ремонта.
11. Масляный насос. Ресурс масляного насоса в основном
определяют качества моторного масла и фильтрующего элемента, поэтому диапазон
его «пробега» весьма широк и на практике составляет от 120 до 350 тыс. км.
Насос ремонтопригоден. Восстановление производят путем замены его рабочих
шестерен и приводной оси, но, как показывает практика, из-за того, что в
запчасти поставляются довольно некачественные детали, его лучше поменять в
сборе.
12. Промежуточный валик и шестерня привода масляного насоса.
Промежуточный валик (в народе: «поросе—
нок») служит 200–250 тыс. км, затем его опорные шейки перешлифовываются
на ремонтный размер (с уменьшением по диаметру на 0,3 мм). Как показывает практика, рекомендуется именно ремонтировать «родной», проверенный в работе валик,
а не покупать новый, качество основной массы которых крайне низкое.
Шестерня привода масляного насоса служит около 100 тыс. км
(у первых моделей ВАЗа ресурс превышал 200 тыс. км). Причиной отказа привода
является износ внутренних зубчиков шестерни, как следствие одновременно
отказывают насос инфраструктуры смазки и распределитель инфраструктуры зажигания.
13. Помпа «инфраструктуры охлаждения. Ресурс помпы в основном
зависит от ресурса ее подшипникового узла и составляет около 200 тыс. км. Узел
полностью ремонтопригоден, к тому же в запасные части поставляется передняя
часть помпы с подшипниковым узлом и крыльчаткой в сборе, что значительно
упрощает ее ремонт. Для того чтобы обеспечить ее «долголетие», необходимо
правильно выставить номинальный зазор крыльчатка — корпус путем подбора толщины
прокладки.
14. Прокладки двигателя. Ресурс разного рода прокладок
существует до первой разборки, конечно, можно их обезжирить, дополнительно
покрыть слоем герметика, но это больше пригодно для ремонта на дороге, чем в
гаражных условиях. Прокладка головки блока цилиндров однозначно меняется во
время демонтажа ГВЦ независимо от пробега.
15. Сальники двигателя. Сальники при капитальном ремонте
двигателя, несмотря на их внешне приличное состояние, менять необходимо всегда.
Особенно это касается заднего сальника коленчатого вала, замена того
связана с крупными затратами времени и средств. Что касается их ресурса, то он
примерно равнозначен (100–150 тыс. км.) и выход из строя одного из них является
сигналом к покупке и скорой замене остальных.
16. Сальники клапанов. В отличие от остальных сальников,
сальники клапанов, кроме истирающего, подвержены еще и сильному температурному
воздействию, поэтому приходят в негодность еще до капитального ремонта
двигателя.
Как показывает практика ремонта, ресурс таких сальников
составляет от 20 до 100 тыс. км и в основном зависит от материала и фирмы-производителя.
Подделки же «ходят» в основном не более 10 тыс. км.
Перегрев головки блока цилиндров, даже возникший единожды,
способен безвозвратно вывести из строя любые сальники клапанов. В таких случаях
структура материала меняется настолько, что по твердости он мало отличается от
обычной пластмассы.
17. Генератор. Ресурс генератора зависит от качества его
подшипников и составляет 120–300 тыс. км, после чего подшипники можно поменять.
В процессе эксплуатации раньше этой операции производят замену щеток. Работа
эта простейшая, без разборки и снятия узла, и не требующая высокой
квалификации, поэтому ресурс щеток обычно не сопоставляется с ресурсом
генератора.
После смены нескольких комплектов подшипников возникает
потребность в проточке или замене контактных колец ротора.
18. Стартер. Стартер работает в гораздо более тяжелых
условиях, чем его «собрат» по бортовой сети — генератор, поэтому его срок
службы до ремонта, несмотря на кратковременность работы, несколько меньше.
Ресурс стартера находится в прямой зависимости от состояния
двигателя и аккумулятора, поэтому на автомобилях с одинаковым пробегом его
состояние весьма различно. Первым обычно выходит из строя обгонная муфта или,
как ее еще называют, бендикс. Ее срок службы в среднем составляет 80 тыс. км,
хотя, иногда попадаются экземпляры, вполне работоспособные и после 150 тыс. км.
Примерно таким же ресурсом обладают втулки ротора, причем первой выходит из
строя втулка передней части как наиболее нагруженная. В любом случае замену
втулок производят комплектом, так как повышенный зазор в одной из них
обязательно снижает ресурс другой.
Щетки стартера «выхаживают» в среднем до 100 тыс. км. Что
касается износа контактных ламелей ротора, то их ресурса при своевременном
обслуживании (очистка и выравнивание поверхности) хватает на весь ресурс
двигателя.
19. Топливный насос. Ресурс механического насоса
определяется состоянием его мембран и составляет более 150 тыс. км.
Клапанный механизм не теряет работоспособности в среднем до
250 тыс. км.
Ресурс топливного насоса впрыскового двигателя не меньше,
чем у его мембранного собрата, но он сильно зависит от загрязненности топлива
(так как все топливо пропускает для охлаждения обмоток через себя).
При эксплуатации впрыскового автомобиля никогда не
допускайте, чтобы бензиновый бак был пустым, в противном случае насос может
быть безвозвратно поврежден от перегрева при первых попытках запуска двигателя
без топлива. К таким же последствиям приводит полностью забитая грязью сетка
топливозаборника.
20. Карбюратор. Ресурс основной массы карбюраторов довольно
большой. Первое, что выходит из строя в подавляющем большинстве карбюраторов
(включая импортные), это мембрана пускового устройства. Ее срок службы обычно
составляет около 100–150 тыс. км. Диафрагма ускорительного насоса, как правило,
«живет» в два раза дольше. Что касается диафрагмы привода вторичной камеры
(там, где она есть), ее ресурса обычно хватает на весь срок службы карбюратора.
21. Распределитель зажигания (в народе — трамблер)
изнашивается в основном в нескольких местах:
1. Сопряжение валик привода — втулка.
2. Износ подшипника подвижной пластины.
3. Прогорание изоляции высоковольтных частей.
4. Повреждение вакуумного регулятора.
5. Износ центробежного регулятора.
6. Подгорание контактной подгруппы (если она есть). Первое, что
приходит в негодность в распределителе
зажигания, это контактная группа, далее изнашивается
подшипник опорной пластины, затем обычно проявляются поломки изоляции
высоковольтных частей (крышка и бегунок), после этого появляется излишний зазор
во втулках и завершают список механизмы опережения зажигания (центробежный и
вакуумный). Как правило, распределитель до пробега в 100–120 тыс. км своими
неисправностями практически не беспокоит. В связи с этим возникает вопрос:
сильно изношенный распределитель ремонтировать или заменить на новый?
Как показывает практика, кустарно отремонтированные
распределители зажигания служат недолго, а ремонт в специализированной
мастерской нередко сопоставим по стоимости с новым узлом, поэтому есть смысл
приобрести новый трамблер в сборе.
22. Датчики двигателя. Датчики весьма долговечны и особых
хлопот во время эксплуатации не вызывают.
Единственный датчик на отечественных автомобилях, который
частенько «барахлит», это датчик включения вентилятора инфраструктуры охлаждения.
Ресурс его не предсказуем вследствие нестабильности качества изготовления. Как
временный выход из положения, концы проводов, подходящие к датчику включения
электрического вентилятора, удлиняют, заводят в салон и подключают к клеммам
второстепенного выключателя (к примеру, обогревателя заднего стекла, временно
его отсоединив), при этом вентилятор включается вручную, когда стрелка
указателя температуры приближается к красной зоне.
Кроме традиционной замены датчика, существует более
радикальный способ — собрать несложный электронный блок, сигнал на который
поступает с датчика указателя температуры двигателя, что позволит надолго
забыть о досаждающем дефекте.
Наша команда специалистов с радостью выполнит переборку
двигателей во Фрязино. Качество гарантировано и поможем подобрать лучшие
запчасти.
Немало поэкспериментировав с различными схемными решениями, «на
вооружение» была принята простая и одновременно удачная схема, опубликованная в
журнале «Радиолюбитель» № 8 за 1996 г. (рис. 1.10).
Немного доработанная схема состоит из: триггера Шмит-та,
собранного на транзисторах VT1, VT2 (КТ315Б), вход того подключен
непосредственно к датчику температуры двигателя Rl (ТМ106), электронного ключа
на транзисторе VT3 (КТ816А) и исполнительного реле К1 (111.37.47 или
112.37.47). Подстроенным резистором R2 устанавливается порог срабатывания реле
при температуре жидкости 92...94°С. Стабилитрон VD1 (Д814Г-Д либо Д813)
препятствует ложным включениям двигателя при колебаниях бортового напряжения.
.

|